Category: Construction Costs
Our Webinar, and Penn Reconstruction
Our webinar about the train station 3D model went off successfully. I was on video for a little more than two hours, Michael a little less; the recording is on YouTube, and I can upload the auto-captioning if people are okay with some truly bad subtitles.
I might even do more webinars as a substitute for Twitch streams, just because Zoom samples video at similar quality to Twitch for my purposes but at far smaller file size; every time I upload a Zoom video I’m reminded that it takes half an hour to upload a two-hour video whereas on Twitch it is two hours when I’m in Germany. (Internet service in other countries I visit is much better.)
The questions, as expected, were mostly not about the 3D model, but about through-running and Penn Station in general. Joe Clift was asking a bunch of questions about the Hudson Tunnel Project (HTP) and its own issues, and he and others were asking about commuter rail frequency. A lot of what we talked about is a preview of a long proposal, currently 19,000, by the Effective Transit Alliance; the short version can be found here. For example, I briefly mentioned on video that Penn Expansion, the plan to demolish a Manhattan block south of Penn Station to add more tracks at a cost of $17 billion, provides no benefits whatsoever, even if it doesn’t incorporate through-running. The explanation is that the required capacity can be accommodated on four to five tracks with best American practices for train turnaround times and with average non-US practices, 10 minutes to turn; the LIRR and New Jersey Transit think they need 18-22 minutes.
There weren’t questions about Penn Reconstruction, the separate (and much better) $7 billion plan to rebuild the station in place. The plan is not bad – it includes extra staircases and escalators, extra space on the lower concourse, and extra exits. But Reinvent Albany just found an agreement between the various users of Penn Station for how to do Penn Reconstruction, and it enshrines some really bad practices: heavy use of consultants, and a choice of one of four project delivery methods all of which involve privatization of the state; state-built construction is not on the menu.
In light of that, it may make sense to delay Penn Reconstruction. The plan as it is locks in bad procurement practices, which mean the costs are necessarily going to be a multiple of what they could be. It’s better to expand in-house construction capacity for the HTP and then deploy it for other projects as the agency gains expertise; France is doing this with Grand Paris Express, using its delivery vehicle Société du Grand Paris as the agency for building RER systems in secondary French cities, rather than letting the accumulated state capacity dissipate when Grand Paris Express is done.
This is separate from the issue of what to even do about Penn Station – Reconstruction in effect snipes all the reimaginings, not just ours but also ones that got more established traction like Vishaan Chakrabarti’s. But even then it’s not necessarily a bad project; it just really isn’t worth $7 billion, and the agreement makes it clear that it is possible to do better if the agencies in question learn what good procurement practices are (which I doubt – the MTA is very bought in to design-build failure).
Mineta Shows How not to Reduce Construction Costs
There’s a short proposal just released by Joshua Schank and Emma Huang at the Mineta Transportation Institute, talking about construction costs. It’s anchored in the experience of Los Angeles more than anything, and is a good example of what not to do. The connections the authors have with LA Metro make me less confident that Los Angeles is serious about reforming in order to be able to build cost-effective infrastructure. There are three points made in the proposal, of which two would make things worse and one would be at best neutral.
What’s in the proposal?
The report links to the various studies done about construction cost comparison, including ours but also Eno’s and Berkeley Law’s. It does so briefly, and then says,
Often overlooked are the inefficiencies and shortcomings inherent in the transportation planning process, which extend far beyond cost, to the quality of the projects, outcomes for the public, and benefits to the region. Rather than propose sweeping, but politically unfeasible, policy changes to address these issues, we focused on more attainable steps that agencies can take right now to improve the process and get to better outcomes.
Mineta’s more attainable steps, in lieu of what we say about project delivery and standardization, are threefold:
- Promise Outcomes, not Projects: instead of promising a concrete piece of infrastructure like a subway, agencies should promise abstract things: “mode-agnostic mobility solutions that ‘carried x riders per day’ or ‘reduced emissions by x%’ or ‘reduced travel time by x minutes,'” which may be “exclusive bus lanes, express bus services, or microtransit.”
- Separate the Planning and Environmental Processes: American agencies today treat the environmental impact statement (EIS) process as the locus of planning, and instead should separate the two out. The planning process should come first; one positive example is the privatized planning of the Sepulveda corridor in Los Angeles.
- Integrate Planning, Construction, and Operations Up Front: different groups handling operations and construction are siloed in the US today, and this should change. There are different ways to do it, but the report spends the longest time on a proposal to offload more responsibilities to public-private partnerships (PPPs or P3s), which should be given long-term contracts for both construction and maintenance.
Point #2 is not really meaningful either way, and the Sepulveda corridor planning is not at all a good example to learn from. The other two points have been to various extents been done before, always with negative consequences.
What’s the problem with the proposal?
Focusing on outcomes rather than projects is called functional procurement in the Nordic countries. The idea is that the state should not be telling contractors what to do, but only set broad goals, like “we need 15,000 passengers per hour capacity.” It’s a recent reform, along many others aiming to increase the role of the private sector in planning.
In truth, public transport is a complex enough system that it’s not enough to say “we need X capacity” or “we need Y speed.” Railways have far too many moving parts, to the point that there’s no alternative to just procuring a system. Too many other factors depend on whether it is a full metro, a tramway, a tram-train (in practice how American light rail systems function), a subway-surface line, or a commuter train. In practice, functional procurement in Sweden hasn’t brought in any change.
In the case of Sepulveda, LA Metro did send some of the high-level P3 proposals to Eric and me. What struck me was that the vendors were proposing completely different technologies. This is irresponsible planning: Sepulveda has a lot of different options for what to do to the north (on the San Fernando Valley side) and south (past LAX), and not all of them work with new technology. For example, one option must be running it through to the Green Line on the 105, but this is only viable if it’s the same light rail technology.
The alternative of microtransit is even worse. It does not work at scale; over a decade of promises by taxi companies that act like tech companies have failed to reduce the cost structure below that of traditional taxis. However, it does open the door for politicians who think they’re being innovative to bring in inefficient non-solutions that are getting a lot of hype. The report brings the example of a New York politician who was taking credit for (small) increases in subway frequency; well, many more politicians spent the 2010s saying that San Francisco’s biggest nonprofit, Uber, was the future of transportation.
The point recommending P3s for their integration of operations and infrastructure is even worse. The privatization of state planning has been an ongoing process in certain parts of the world – it’s universal in the English-speaking world and advancing in the Nordic countries. The outcomes are always the same: infrastructure construction gets worse.
The top-down Swedish state planning of the third quarter of the 20th century built around 104 km of the T-bana, of which 57 are underground, for $3.6 billion in 2022 prices. The present process, negotiated over decades with people who don’t like an obtrusive state and are inspired by British privatization, is building about 19 underground km, for $4.5 billion. This mirrors real increases in absolute costs (not just overruns) throughout Scandinavia. The costs of Sweden in the 1940s-70s were atypically low, but there’s no need for them to have risen so much since then; German costs have been fairly flat over this period, Italian costs rose to the 1970s-80s due to corruption and have since fallen, Spanish costs are still very low.
As we note in the Swedish case report, Nordic planners take it for granted that privatization is good, and ding Germany for not doing as much of it as the UK; of these two countries, one can build and one can’t, and the one that can is unfortunately not the one getting accolades. The United Kingdom, was building subways for the same costs as Germany and Italy in the 1960s and 70s, but its real costs have since grown by a factor of almost four. I can’t say for certain that it’s about Britain’s love affair with P3s, but the fact that the places that use P3s the most are the worst at building infrastructure should make people more critical of the process.
Britain Remade’s Report on Construction Costs
The group Britain Remade dropped a report criticizing Britain for its high infrastructure construction costs three days ago. I recommend everyone read Sam Dumitriu and Ben Hopkinson’s post on the subject. Sam and Ben constructed their own database. Their metro tunneling costs mostly (but not exclusively) come from our database but include more detail such as the construction method used; in addition, they have a list of tram projects, another list of highway projects, and a section about rail electrification. Over the last three days, this report has generated a huge amount of discussion on Twitter about this, with appearances in mainstream media. People have asked me for my take, so here it is. It’s a good report, and the recommendations are solid, but I think it would benefit from looking at historical costs in both the US and UK. In particular, while the report is good, the way it’s portrayed in the media misses a lot.
What’s in the report
Sam and Ben’s post talks about different issues, affecting different aspects of the UK, all leading to high costs:
NIMBYism
The report brings up examples of NIMBYs slowing down construction and making it more expensive, and quotes Brooks-Liscow on American highway cost growth in the 1960s and 70s. This is what has been quoted in the media the most: Financial Times call it the “NIMBY tax,” and the Telegraph spends more time on this than on the other issues detailed below.
The NIMBYs have both legal and political power. The legal power comes from American-style growth in red tape; the Telegraph article brings up that the planning application for a highway tunnel under the Thames Estuary is 63,000 pages long and has so far cost 250 million £ in planning preparations alone (the entire scheme is 9 billion £ for 23 km of which only 4.3 are in tunnel). The political power is less mentioned in the report, but remains important as well – High Speed 2 has a lot of gratuitous tunneling due to the political power of the people living along the route in the Home Counties.
Start-and-stop construction
British rail electrification costs are noticeably higher than Continental European ones. The report points out that construction is not contiguous but is rather done in starts and stops, leading to worse outcomes:

Lack of standardization
Sam and Ben bring up the point Bent Flyvbjerg makes about modularization and standardization. This is the least-developed point in the report, to the point that I’m not sure this is a real problem in the United Kingdom. It is a serious problem in the United States, but while both American and British costs of infrastructure construction are very high, not every American problem is present in the UK – for example, none of the British consultants we’ve spoken to has ever complained about labor in the UK, even though enoguh of them are ideologically hostile to unions that they’d mention it if it were as bad as in the US.
What’s not in the report?
There are some gaps in the analysis, which I think compromise its quality. The analysis itself is correct and mentions serious problems, but would benefit from including more things, I believe.
Historical costs
The construction costs as presented are a snapshot in time: in the 21st century, British (and Canadian, and American) costs have been very high compared with Continental Europe. There are no trends over time, all of which point to some additional issues. In contrast, I urge people to go to my post from the beginning of the year and follow links. The biggest missing numbers are from London in the 1960s and 70s: the Victoria and Jubilee lines were not at all atypically expensive for European subway tunnels at the time – at the time, metro construction costs in London, Italian cities, and German cities were about the same. Since then, Germany has inched up slightly, Italy has gone down due to the anti-corruption laws passed in the 1990s, and the United Kingdom has nearly quadrupled its construction costs over the Jubilee, which was already noticeably higher than the Victoria.
The upshot is that whatever happened that made Britain incapable of building happened between the 1970s and the 1990s. The construction cost increase since the 1990s has been real but small: the Jubilee line extension, built 1993-9, cost 218.7 million £/km, or 387 million £/km in 2022 prices; the Northern line extension, built 2015-21, cost 375 million £/km, or 431 million £/km in 2022 prices. The Jubilee extension is only 80% underground, but has four Thames crossings; overall, I think it and the Northern extension are of similar complexity. It’s a real increase over those 22 years; but the previous 20 years, since the original Jubilee line (built 1971-9), saw an increase to 387 million £/km from 117 million £/km.
The issue of soft costs
Britain has a soft costs crisis. Marco Chitti points out how design costs that amount to 5-10% of the hard costs in Italy (and France, and Spain) are a much larger proportion of the overall budget in English-speaking countries, with some recent projects clocking in at 50%. In the American discourse, this is mocked as “consultants supervising consultants.” Every time something is outsourced, there’s additional friction in contracting – and the extent of outsourcing to private consultants is rapidly growing in the Anglosphere.
On Twitter, some people were asking if construction costs are also high in other Anglo countries, like Australia and New Zealand; the answer is that they are, but their cost growth is more recent, as if they used to be good but then learned bad practices from the metropole. In Canada, we have enough cost history to say that this was the case with some certainty: as costs in Toronto crept up in the 1990s, the TTC switched to design-build, supposed inspired by the Madrid experience – but Spain does not use design-build and sticks to traditional design-bid-build; subsequently, Toronto’s costs exploded, going, in 2022 prices, from C$305 million/km for the Sheppard line to C$1.2 billion/km for the Ontario Line. Every cost increase, Canada responds with further privatization; the Ontario Line is a PPP. And this is seen the most clearly in the soft cost multiplier, and in the rise in complaints among civil servants, contractors, and consultants about contracting red tape.
Britain Remade’s political recommendations
Britain Remade seems anchored not in London but in secondary cities, judging by the infrastructure projects it talks most about. One of its political recommendations is,
Britain is one of the most centralised countries in the world. Too often, Westminster prioritises investments in long-distance intercity rail such as HS2 or the Northern Powerhouse Rail when they would be better off focusing on cutting down commuting times. Local leaders understand local priorities better than national politicians who spend most of their time in Westminster. If we really devolved power and gave mayors real powers over spending, we’d get the right sort of transport more often.
Britain Remade is campaigning for better local transport. We want to take power from Westminster and give it to local leaders who know better. But, we also want to make sure transport investment stretches further. That’s why we are calling for the government to copy what other countries do to bring costs down, deliver projects on time, and build more.
https://www.britainremade.co.uk/building_better_local_transport
Devolution to the Metropolitan counties – those covering Birmingham, Manchester, Liverpool, Leeds, Sheffield, and Newcastle – has been on the agenda in the UK for some time now. This reform is intended to give regions more power over spending, inspired by the success of devolution to London, where Transport for London has good operating practices and plenty of in-house capacity. More internationally-minded Brits (that is, to say, European-minded – there’s little learning from elsewhere except when consultants treat Singapore and Hong Kong as mirrors of their own bad ideas) will even point out the extensive regional empowerment in the Nordic countries: Swedish counties have a lot of spending power, and it’s possible to get all stakeholders in the room together in a county.
And yet, the United States is highly decentralized too, and has extreme construction costs. Conversely, Britain knew how to build infrastructure in the 1960s and 70s, under a centralized administrative state. Devolution to the Metropolitan counties will likely lead to good results in general, but not in infrastructure construction costs.
The media discourse
The report raises some interesting points. The start-and-stop nature of British electrification is a serious problem. To this, I’ll add that in Denmark, electrification costs are higher than in peer Northern European countries because its project, while more continuous, suffered from political football and was canceled and then uncanceled.
Unfortunately, all media discussion I can see, in the mainstream as well as on Twitter, misses the point. There’s too much focus on NIMBYism, for one. Britain is not the United States. In the United States, the sequence is that first of all the system empowered NIMBYs politically and legally starting in the 1960s and 70s, and only then did it privatize the state. In the United Kingdom, this is reversed: the growth in NIMBY empowerment is recent, with rapid expansion of the expected length of an environmental impact statement, and with multiplication of conflicting regulations – for example, there are equity rules requiring serving poor and not just rich neighborhoods, but at the same time, there must be a business case, and the value of time in the British benefit-cost analysis rules is proportional to rider income. This explosion in red tape is clearly increasing cost, but the costs were very high even before it happened.
Then, there are the usual incurious ideas from the Twitter reply gallery, including some people with serious followings: Britain must have stronger property rights (no it doesn’t, and neither does the US; look at Japan instead), or it’s related to a general cost disease (British health care costs are normal), or what about Hong Kong (it’s even more expensive).
Pete Buttigieg, Bent Flyvbjerg, and My Pessimism About American Costs
A few days ago, US Secretary of Transportation Pete Buttigieg appeared together with Bent Flyvbjerg to discuss megaprojects and construction costs. Flyvbjerg’s work on cost overruns is, in the English-speaking world, the starting point for any discussion of infrastructure costs, and I’m glad that it is finally noticed at such a high level.
Unfortunately, everything about the discussion, in context, makes me pessimistic. The appearance was about establishing a Center of Excellence at the Volpe Center to study project delivery and transmit best practices to various agencies; but, in context with what I’ve seen at agencies as well as federal regulators, it will not be able to figure out how to learn good practices the way it is currently set up, and what it can learn, it won’t be able to transmit. It’s sad, really, because Buttigieg clearly wants to be able to build; with his current position and presidential ambitions, his path upward relies on being able to build transportation megaprojects, but the current US Department of Transportation (USDOT) and the political system writ large seem uninterested in reforming in the right direction.
What Flyvbjerg said
Flyvbjerg’s studies are predominantly about cost overruns, rather than absolute costs. The insights required to limit overruns are not the same as those required to reduce costs in general, but they intersect substantially, and in recent years Flyvbjerg has written more about absolute costs as well. The topics he discussed with Buttigieg are in this intersection.
In latter-day Flyvbjerg, there’s a great emphasis on standardization and modularity. He speaks favorably of Spain’s standardized construction methods as one reason for its famously low construction costs – costs that remain very low in the 2020s. We found something similar in our own work, seeing an increase of 50% in New York construction costs coming from lack of standardization in track and station systems; in our own organization, we conceive of standardization as a design standard, separate from the issue of project delivery, but fundamentally it’s all about how to deliver infrastructure construction cost-effectively.
To an extent, the American public-sector transportation project managers I know are aware of the issue of modularity, and are trying to apply it at various levels. However, they are hampered both by obstructive senior managers and political appointees and by federal regulations. For example, to build commuter rail stations, modular design requires technology that, due to supply chain issues, is not made in the United States; this requires a waiver from Buy America rules, which should be straightforward since “not made in the US” is a valid legal reason, but the relevant federal regulatory body is swamped with requests and takes too long to process them, and the federal regulators we spoke to were sympathetic but didn’t seem interested in processing requests faster.
But Flyvbjerg goes further than just asking for design modularity. He uses the expression “You’re unique, like everybody else.” He talks about learning from other projects, and Buttigieg seems to get it. This is really useful in the sense that nothing that is done in the United States is globally unique; California High-Speed Rail, among the projects they discussed, was an attempt to import technology that already 15 years ago had a long history in Western Europe and Japan. But that project was still planned without any attempt to learn the successful project delivery mechanisms of those older systems. And the Volpe Center, federal regulators, and federal politicos writ large seem uninterested in foreign learning even now.
What we’ve seen
Eric, Elif, Marco, and I have presented our findings to Americans at various levels – not to Buttigieg himself, but to people who I think may regularly interact with him; I can’t tell the exact level, not being familiar with government insider culture. Some of the people we’ve interacted with seem helpful, interested in adopting some of our findings, and willing to change things; others are not.
But what we’ve persistently seen is an unwillingness to just go ahead and learn from foreigners. The new Center of Excellence is run by Cynthia Maloney, who’s worked for Volpe and DOT since 2014 and worked for NASA before; I know nothing of her, but I know what she isn’t, which is an experienced transportation professional who has delivered cost-effective projects before, a type of person who does not exist in the United States and barely exists in the rest of the English-speaking world.
And there’s the rub. We’ve talked to Americans at these levels – regulators, agency heads, political advisors, appointees – and they are often interested in issues of procurement reform, interagency coordination, modular design, and so on. But when we mention the issue of learning from outside the US, they react negatively:
- They rarely speak foreign languages or respect people who do, and therefore don’t try to read the literature if it’s not written in English, such as the Cour des Comptes report on Grand Paris Express.
- They have no interest in hiring foreigners with successful experience in Europe or Asia – the only foreigner whose name comes up is Andy Byford, for his success in New York.
- They don’t ever follow up with specifics that we bring up about Milan or Stockholm, let alone Istanbul, which Elif points out they don’t even register as a place that could be potentially worth looking at.
- They sometimes even make excuses for why it’s not possible to replicate foreign success, in a way that makes it clear they haven’t engaged with the material; for a non-transportation example, a New York sanitation communications official said, with perfect confidence, that New York cannot learn from Rome, because Rome was leveled during WW2 (in fact, Rome was famously an open city).
Even the choice of which academics to learn from exhibits this bias. Flyvbjerg is very well-known in the English-speaking world as well as in countries that speak perfect nonnative English, including his own native Denmark, the rest of Scandinavia, and the Netherlands. But in Germany, France, and Southern Europe, people generally work in the local language, with much lower levels of globalization, and I think this is also the case in East Asia (except high-cost Hong Kong). And there’s simply no engagement with what people here do from the US; the UK appears somewhat better.
You can’t change the United States from a country that builds subways for $2 billion/km in New York and $1 billion/km elsewhere to a country that does so for $200 million/km if all you ever do is talk to other Americans. But the Volpe Center appears on track to do just that. The American political sphere is an extremely insulated place. One of the staffers we spoke to openly told us that it’s hard to sell foreign learning to the American public; well, it’s even harder to sell infrastructure when it’s said to cost $300 billion to turn the Northeast Corridor into a proper high-speed line, where here it would cost $20 billion. DOT seems to be choosing, unconsciously, not to have public transportation.
Assume Normal Costs: An Update
The maps below detail what New York could build if its construction costs were normal, rather than the highest in the world for reasons that the city and state could choose to change. I’ve been working on this for a while – we considered including these maps in our final report before removing them from scope to save time.
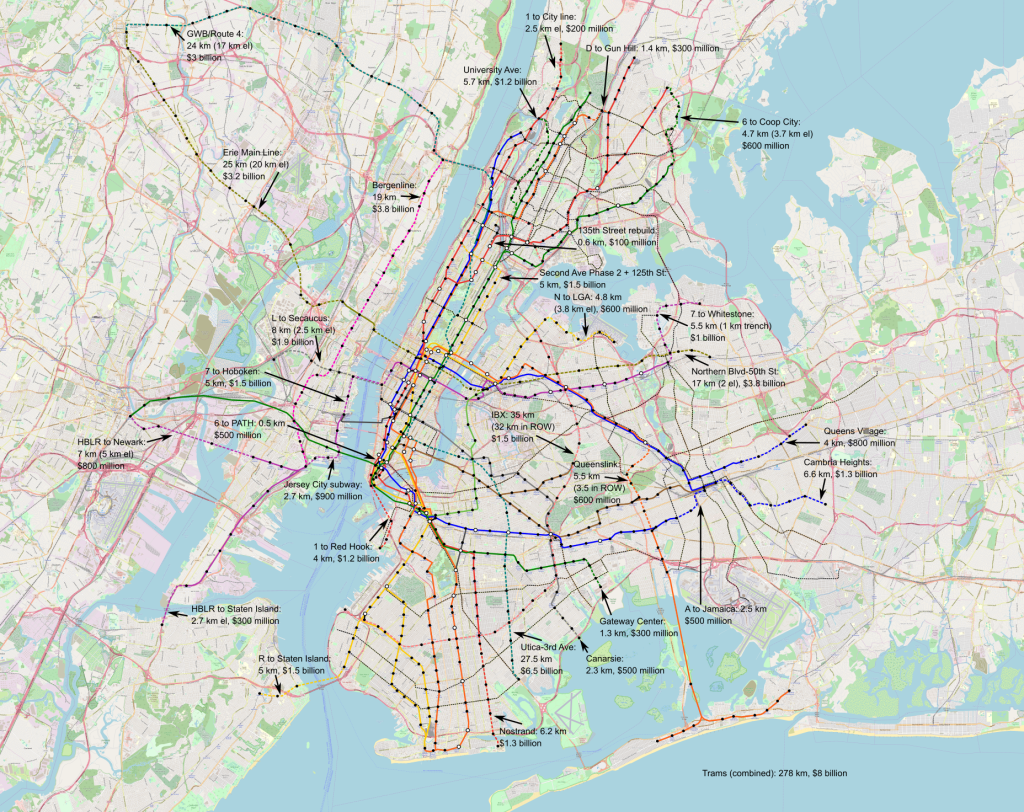
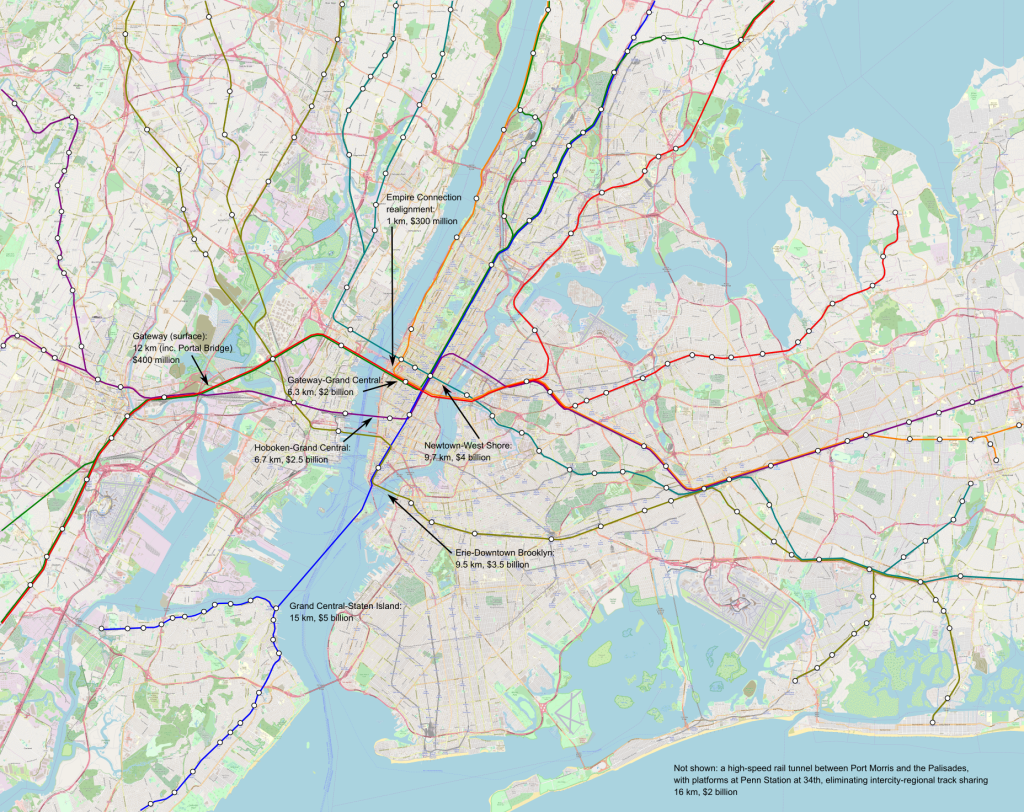
Higher-resolution images can be found here and here; they’re 53 MB each.
Didn’t you do this before?
Yes. I wrote a post to a similar effect four years ago. The maps here are updated to include slightly different lines – I think the new one reflects city transportation needs better – and to add light rail and not just subway and commuter rail tunnels. But more importantly, the new maps have much higher costs, reflecting a few years’ worth of inflation (this is 2022 dollars) and some large real cost increases in Scandinavia.
What’s included in the maps?
The maps include the following items:
- 278 km of new streetcars, which are envisioned to be in dedicated lanes; on the Brooklyn and Queensborough Bridges, they’d share the bridges’ grade separation from traffic into Manhattan, which in the case of the Brooklyn Bridge should be an elevated version of the branched subway-surface lines of Boston, Philadelphia, San Francisco, and most German cities. Those should cost $8 billion in total, based on Eno’s European numbers plus some recent urban German projects.
- 240 km of new subway lines, divided as 147.6 km in the city (97.1 km underground) and 92.4 km across the Hudson and in New Jersey (45.2 km underground). Of those 240 km, 147.5 km comprise four new trunk lines, including the already-planned IBX, and the rest are extensions of existing lines. Those should cost $25.2 billion for the city lines and $15.4 billion for the New Jersey lines.
- Rearrangement of existing lines to reduce branching (“deinterlining“) and improve capacity and schedule robustness; the PATH changes are especially radical, turning the system into extensions of the 6 and 7 trains plus a Hoboken-Herald Square shuttle.
- 48.2 km of commuter rail tunnels, creating seven independent trunk lines across the region, all running across between suburbs through the Manhattan core. In addition to some surface improvements between New York and Newark, those should cost $17.7 billion, but some additional costs, totaling low single-digit billions, need to be incurred for further improvements to junctions, station platforms, and electrification.
The different mode of transportation are intended to work together. They’re split across two maps to avoid cluttering the core too much, but the transfers should be free and the fares should be the same within each zone (thus, all trains within the city must charge MetroCard/OMNY fare, including commuter rail and the JFK AirTrain). The best way to connect between two stations may involve changing modes – this is why there are three light rail lines terminating at or near JFK not connecting to one another except via the AirTrain.
What else is included?
There must be concurrent improvements in the quality of service and stations that are not visible on a map:
- Wheelchair accessibility at every station is a must, and must be built immediately; a judge with courage, an interest in improving the region, and an eye for enforcing civil rights and accessibility laws should impose a deadline in the early to mid 2030s for full compliance. A reasonable budget, based on Berlin, Madrid, and Milan, is about $10-15 million per remaining station, a total of around $4 billion.
- Platform edge doors at every station are a good investment as well. They facilitate air conditioning underground; they create more space on the platform because they make it easier to stand closer to the platform edge when the station is crowded; they eliminate deaths and injuries from accidental falls, suicides, and criminal pushes. The only data point I have is from Paris, where pro-rated to New York’s length it should be $10 million per station and $5 billion citywide.
- Signaling must be upgraded to the most modern standards; the L and 7 trains are mostly there already, with communications-based train control (CBTC). Based on automation costs in Nuremberg and Paris, this should be about $6 billion systemwide. The greater precision of computers has sped up Paris Métro lines by almost 20% and increased capacity. Together with the deinterlining program, a single subway track pair, currently capped at 24 trains an hour in most cases, could run about 40 trains per hour.
- Improvements in operations and maintenance efficiency don’t cost money, just political capital, but permit service to be more reliable while cutting New York’s operating expense, which are 1.5-2.5 time a high as the norm for large first-world subway systems.
The frequency on the subway and streetcar lines depicted on the map must conform to the Six-Minute Service campaign demand of Riders Alliance and allies. This means that streetcars and subway branches run very six minute all day, every day, and subway trunk lines like the 6, 7, and L get twice as much frequency.
What alternatives are there?
Some decisions on the map are set in stone: an extension of Second Avenue Subway into Harlem and thence west along 125th Street must be a top priority, done better than the present-day project with it extravagant costs. However, others have alternatives, not depicted.
One notable place where this could easily be done another way is the assignment of local and express trains feeding Eighth and Sixth Avenues. As depicted, in Queens, F trains run local to Sixth Avenue and E trains run express to Eighth; then, to keep the local and express patterns consistent, Washington Heights trains run local and Grand Concourse trains run express. But this could be flipped entirely, with the advantage of eliminating the awkward Jamaica-to-Manhattan-to-Jamaica service and replacing it with straighter lines. Or, service patterns could change, so that the E runs express in Queen and local in Manhattan as it does today.
Another is the commuter rail tunnel system in Lower Manhattan. There are many options for how to connect New Jersey, Lower Manhattan, and Brooklyn; I believe what I drew, via the Erie Railroad’s historic alignment to Pavonia/Newport, is the best option, but there are alternatives and all must be studied seriously. The location of the Lower Manhattan transfer station likewise requires a delicate engineering study, and the answer may be that additional stops are prudent, for example two stops at City Hall and South Ferry rather than the single depicted station at Fulton Street.
What are those costs?
I encourage people to read our costs report to look at what goes into the numbers. But, in brief, we’ve identified a recipe to cut New York subway construction costs by a factor of 9-10. On current numbers, this means New York can cut its subway construction costs to $200-250 million per kilometer – a bit less in the easiest places like Eastern Queens, somewhat more in Manhattan or across water. Commuter rail tunnel costs are higher, first because they tend to be built only in the most difficult areas – in easier ones, commuter rail uses legacy lines – and second because they involve bigger stations in more constrained areas. Those, too, follow what we’ve found in comparison cases in Southern Europe, the Nordic countries, Turkey, France, and Germany.
In total, the costs so projected on the map, $66.3 billion in total, are only slightly higher than the total cost of Grand Paris Express, which is $60 billion in 2022 dollars. But Paris is also building other Métro, RER, and tramway extensions at the same time; this means that even the program I’m proposing, implemented over 15 years, would still leave New York spending less money than Paris.
Is this possible?
Yes. The governance changes we outline are all doable at the state level; federal officials can nudge things and city politician can assist and support. There’s little confidence that current leadership even wants to build, let alone knows what to do, but it’s all doable, and our report linked in the lede provides the blueprint.
Quick Note: Los Angeles Spends $50,000 Per Bus Shelter
I saw a few months ago that Los Angeles was planning to equip its entire bus network with shelter, and rejoiced that such an underrated amenity finally gets the attention it deserves. Unfortunately, the cost of the program is now $50,000 per bus shelter; to lower the cost, the city is experimenting with a substandard shelter providing no protection from the elements for $10,000. In Victoria, as pointed out by one commenter on Twitter, a full shelter is around $15,000 in 2018 Canadian dollars, comparable to 2023 American ones.
Ordinarily, it would be a dog-bites-man story: of course the costs are at a premium of a factor of three over Canada (let alone a place that builds cheaply), it’s an American transit infrastructure project. But this one is significant because bus shelter is small in scope – it’s not a megaproject, and this means that rules of megaprojects do not apply to it.
For example, installing shelter at thousands of stops, as Los Angeles is doing, allows for repetition of a standard design that vendors can figure out on their own. This means that the usual privatization of decisionmaking should not be a problem. (It’s been pointed out to me that design-build works well for municipal parking garages, since they’re so streamlined at this point.)
Moreover, bus shelter, even repeated so many times, is still small enough scope that a small in-house team could handle it. LACMTA has been talking to us about how to scale up their in-house team, and we couldn’t give them concrete numbers, but I believe what they have for design review is in the teens, which is probably not enough for a subway extension but should be for a bus shelter program measured in the tens of millions of dollars or (with the cost blowouts factored in) very low hundreds of millions. Elsewhere, for example in Boston, we’ve seen agencies build small things affordably – Boston’s premium over Berlin for building infill commuter rail stations is a factor of maybe 1.5 – and fail at building large things such as urban rail expansion, because their design review team is sized for small and not large things.
Finally, there’s a problem with politicization, in which when politicians insert themselves into a piece of infrastructure, hoping to make it their legacy, it will end up raising costs with at best no and at worst negative benefit to users. Small items like this ordinarily do not have this problem, as they fly under the radar of politicians as well as surplus-extracting community groups.
So why is this so expensive?
I don’t know the details of this failure – all I know is a handful of links to the current cost. I suspect, judging by the tone used in press coverage, that it’s politicization. Note that the piece linked in the lead paragraph centers the issue of gender equity; this isn’t stupid (as the other link points out, bus shelter has a disproportionately positive impact on women), but it does suggest someone thought about the political implications of this. The piece also quotes the designers as having developed the new substandard option “with input from female riders,” suggesting some waste on community consultation.
If I’m right on this, then this suggests a great peril for any city that looks at small and large projects, finds that the small ones are more cost-effective, and decides to prioritize them over large ones. In a city that builds subway expansion and also installs bus shelter beneath anyone’s notice, the bus shelter may be achievable at reasonable cost. But as soon as the shelter turns into a splashy program, beloved by incompetent managers who figure it’s within their span of control and by politicians (who are by definition incompetent on managerial issues), it will acquire the same problems of politicization usually associated with megaprojects. In this case, it’s waste coming from community consultation. In other cases, it might be demands for neighborhood signatures, or intransigence by abutting property owners or by utilities figuring there is surplus to extract, or any of the other causes of cost overruns.
And in particular, downgrading your city’s investment plan just because the flashiest items have cost blowouts wouldn’t end the cost blowouts. If you can’t build subways, work on making yourself capable of building subways; avoiding that mess and building other things instead of subways would run into the same problems and soon you’d be paying $50,000 for a single bus shelter.
CNBC Video on Construction Costs
There’s a CNBC video about construction costs. It references our data a bunch, and I’d like to make a few notes about this.
Urban rail and GDP
CNBC opens by saying better urban rail would increase American GDP by 10%, sourcing the claim to our report. This isn’t quite right: our report references Hsieh-Moretti on upzoning in New York and the Bay Area; they estimate that relaxing zoning restrictions in those two regions to the US median starting in 1964 would have, assuming perfect mobility, raised American GDP by 9% in the conditions of 2009 (and the effect size should have grown since).
The relevance of transportation is that the counterfactual involves both regions growing explosively: New York employment grows by 1,010% more than in reality, so by a factor of about five compared with actual 1960s population and about 3.6 compared with actual 2009 (in 1969-2009, metro employment grew 35.4%), and likewise San Francisco would be 3.9 times bigger than in reality in 2009 and San Jose, having had much faster growth in the previous decades in reality, would have still been 2.5 times bigger. Hsieh-Moretti assume infrastructure expands to accommodate this growth. But if it can’t, then the growth in GDP is lower and the growth in consumer welfare is massively lower due to congestion externalities, hence our citation of Devin Bunten’s paper on this subject.
So the issue isn’t really that building subways would increase American GDP by 10%. It’s that building subways paired with transit-oriented development, the latter proceeding at levels that would raise regional population at a somewhat faster rate than in 1900-30, would do so. The issue of costs in the United States is only peripherally connected with the lack of transit-oriented development, an American peculiarity in which more housing is built in poorer regions than in the largest, richest metro areas. In contrast, Canada gets TOD right and yet is rapidly converging to American construction costs, Toronto’s reaching around US$1 billion/km per the latest estimates. Germany, conversely, is rather NIMBY, although its rich cities still build much more than New York or the Bay Area, and is capable of building subways just fine.
The portrayal of Second Avenue Subway
The portrayal looks mostly good. It points out the tension between Second Avenue Subway’s extreme cost per km and reasonable cost per rider, the latter comparing very favorably with Los Angeles and about on a par with Grand Paris Express. Second Avenue Subway Phase 1 was a bad project in the sense that it was severely overbuilt and poorly managed, but were it not possible to build it for cheaper (which it was), it would be a good value proposition, and even Phase 2 is marginal rather than bad. The issue is that New York’s cost-effectiveness frontier, at current costs, makes it capable of building a few km of subway per generation, whereas that of Paris, a city that isn’t especially cheap to build in, enables the 200 km Grand Paris Express.
The video goes over our comparison of station to tunnel costs, and connects this with various forms of surplus extraction; Eric gives examples of how cities demand betterments and do general micromanagement and threaten to withhold permits unless they get what he calls bribes. It gets the picture well for how important actors, up to and including the mayor of New York, just treat infrastructure as an opportunity to grab surplus for other priorities.
There are a few errors, all minor:
- The visualization of Second Avenue Subway has it running down First Avenue in Midtown and Downtown Manhattan, which was certainly not in the original plan and I think still is not.
- The video states the cost of Grand Paris Express at $38 billion, I think out of converting euros to dollars at exchange rate, whereas in PPP terms it’s $47 billion in 2012 prices and $60 billion in 2022 dollars, either way about 10 times the absolute cost of Second Avenue Subway Phase 1 for 10 times the projected ridership and 70 times the overall length. But the costs per rider are correct, at least.
- I’m not sure why, but the Madrid numbers are stated to be around $200 million/km, which is a cost that I don’t think exists there – costs in our database don’t include the latest lines there, but the ongoing expansion program is 40.5 km for 2 billion euros, which in PPP terms is around $70 million/km, I think all underground.
- The section on soft costs says that they were 21% of Second Avenue Subway’s overall costs, compared with a norm of 5-10% elsewhere. This is not quite true – they were 21% of the hard costs (and the same is true of the 5-10% figure); their share of overall costs was therefore a bit lower.
Carmen Bianco and Robert Puentes
Three people are extensively interviewed in the video. The first is Carmen Bianco, who was New York City Transit head in 2013-5. The second is Eric. The third is Eno’s Robert Puentes. The interviews are pretty good (by which I mean those with Bianco and Puentes – I of course find what Eric says good I’m the least impartial judge on this). There’s also a short quote from Bent Flyvbjerg about construction productivity, which isn’t quite true (productivity is rising in Sweden, just at lower rates than general growth).
Puentes talks about standardization, comparing the custom-designed stations in the United States with the standardized ones in Copenhagen. He also talks about the benefits of utilitarian stations and connects this with standardization – American subway and light rail stations aren’t particularly nice (the overbuilding goes to crew break rooms and crossovers, not passenger facilities), but one way local political actors get to feel important is making each station a bit different, and I’m glad he highlights this connection between overbuilding and poor standardization. But I think he somewhat errs in that he says that one cause of this among a few is that American cities build little subway tunneling. Copenhagen, after all, built its first line in the 1990s and early 2000s (using consultants, since there was no preexisting in-house staff and no political appetite to staff up); it just made the right design decision to standardize, which has helped it build a subway even at not especially low costs, in a fairly small city.
Then there’s Bianco, who I think appears talking more than anyone else, even Eric. He gives the standard list of problems in New York: it’s a dense city with a lot of complex underground infrastructure, utility relocation is difficult, and so on. At least on camera, he doesn’t make excuses. It’s just, complex historic utilities are not unique to New York, and I don’t know to what extent he understands that New York can learn this from Italian cities (or from London, which I believe has very good underground utility mapping). I assume Bianco isn’t generally great about this since he was in charge in 2013-5 and didn’t reform this system, but he doesn’t come off as repulsive, and it’s plausible that he’s more reasonable knowing not what he may not have 10 years ago.
I Gave a Followup Talk at TransitCon
Hayden Clarkin’s online conference TransitCon just happened, and I was drafted at the last minute to give a talk about construction costs. Here are the slides; for the most part, they’re a compressed version of slides that regular readers have seen before, except done in Beamer rather than Google Slides.
Cognizant of the fact that most people at TransitCon would have heard of me and our research and many would have read the reports or at least seen me, Eric, Marco, or Elif talk about them, I rushed through the description of our report. Instead of just going over trodden ground, I added slides at the end describing new issues we’d learned about since writing the synthesis, which was in a fairly advanced draft in late summer 2022 already. This fell into two categories: new obstacles, and reactions of people in power.
The new obstacles slide talks about the issue of last-minute squeaking (in the “squeaky wheel gets the grease” aphorism, which can and should be changed to “squeaky wheel gets replaced”). The most glaring examples of gross surplus extraction for Second Avenue Subway and the Green Line Extension all happened fairly early in the process.
In contrast, since then, Eric has spent so much time working in Seattle he could given time make an entire case out of its ongoing problems, and there, some of the extraction has been late in the project: one suburb’s fire department demanded construction in excess of the normal fire codes or else it wouldn’t certify the stations in its jurisdiction as fire-safe. In Dallas, the city itself is grabbing surplus: it’s demanding betterments and holding up the DART Silver Line until it gets them, adding $150,000 a day to the cost of the project. These two examples are both late in the process, after the Full Funding Grant Agreement has been signed; but once there is a political commitment, a local actor can still hope to grab surplus by demanding unreasonable changes.
But it’s really better to view this issue as one of top-level cowardice and unwillingness to take responsibility. The solution in Seattle is not hard: dissolve the department and have it taken over by the state or by Seattle proper. But whoever does that in effect takes ownership of every single fire in the suburb, and this requires taking more responsibility than American politicians and their appointees are used to.
The reaction of people in power plays to how they treat obstacles. I wrote a title for that slide, The Self-Hating State, and then deleted it and replaced it with the less toothy Public Officials and Consultants. But in effect what we see when we present the results to sympathetic federal and state officials who want to do better (i.e. not the MTA) is that most government officials don’t like the government very much. Their eyes glaze over the sort of technical and economic points that their counterparts here talk about, and instead they talk about how consultants have more long-term experience, when most of what the consultants know is how poorly-managed projects are built and where they do have positive knowledge (like the standardization of construction in Copenhagen) they’re not listened to.
Even more frustrating is their reaction to red tape. They take it as a given that the government must involve red tape; the same red tape in the private sector is invisible to them, such as when Seattle-area construction involves multiple jurisdictions each with its own consultants. But more fundamentally, these are people who can rewrite regulations, formally or informally, to make things easier; they just consider a government that works unthinkable.
More on Consultants
We’ve gotten a lot of criticism from various quarters about our analysis and conclusions at the Transit Costs Project. The focus for this post is a criticism that isn’t usually made in public but looks like the biggest one among people in power in the American federal government: the issue of consultants. Writing in Slate about our report, Henry Grabar identified consultants as the ultimate reason the United States can’t build. This should be nuanced in that consultants are one of a few primary reasons, but the broad outline of the complaint is right: the overuse of consultants is a serious problem and must be replaced with large in-house bureaucracies in explicit rejection of the privatization of the state. And yet, there’s pushback. Why, and why is it wrong?
The current situation
In the English-speaking world today, the dominant view of infrastructure is that private companies are inherently more efficient than the state. In service of this ideology, large state organizations were left to rot and then privatized. The historic sequence is generally that as efficiency levels fall, political interest in investing in organizational capacity declines, and in-house organizations take the blame.
American and British societies both believe that specialist experts are inherently suspect and must always lower their gaze in the presence of a generalist who is paid and otherwise treated as a master of the universe, and thus those organizations would receive overclass appointees (US version) or generalist civil servants (UK version) who constantly belittle them and also have little ability to reform them from the inside. It’s remarkable how non-technical the members of the American overclass Eric and I have talked to are; one of them asked us straight out why we didn’t talk to more lawyers in our report where we talked to engineers, planners, procurement experts, and other specialists.
The result of this sequence is that usually at the time of privatization – say, when New York’s MTA let go of its 1,600 strong capital construction department in the early 2000s and downsized by about an order of magnitude – what is left is a hulk, easy pickings for the privatizer. What is left of that is even more of a hulk. The upshot is that in places that rely on consultants in lieu of in-house expertise, the quality of current public-sector leadership (that is, the various state political appointees, most federal political appointees, and even some permanent staff with pure management background) is low. The consultants are individually more competent than them, and this is readily apparent to anyone who’s talked with both sets of people; even the political appointees themselves get it and think their expertise is in managing the consultants.
What the consultants know
When the state doesn’t really like itself and privatizes key functions to consultants, the consultants look more competent. One federal official – not a political appointee, to be clear – told us straight out that the consultants have experience since they work on so many projects, domestically and internationally.
The problem is that what the consultants know is how things work on projects that use consultants. This is how an experienced consultant can say something as obviously wrong as “The standard approach to construction in most of Europe outside Russia is design-build.” Is this even remotely true? No. Parts of Europe are transitioning to design-build under British influence, universally seeing cost increases as they do so, but even in the Nordic countries and France this process is in its infancy, and in nearly all of the rest of Western Europe it’s not done at all. The upshot is that the US/UK consultant sphere is an expert on how to build public transportation in the failed US/UK way, and its international experience is largely (not entirely) US/UK-style badness.
But Americans are an incurious people. Even the ones who are aware of European and rich-Asian success in infrastructure and urbanism only really interact with it as tourists. So they can’t distinguish a government-built program like the TGV or nearly every European subway system from the few that are more consultant-driven like the Copenhagen Metro (at the time of its construction, Scandinavia’s highest-cost metro – though the rest of the Nordic world is catching up in both privatization and costs).
What’s more, the American preference for generalist knowledge means that what they see of the Copenhagen Metro is much more its use of unconventional financing than its use of driverless trains at very high frequency or its standardization of station components. Thus, looking at a metro that for all its expense by its regional standards was also cheaper than anything in the US going back to the 1970s, they take notes and imitate all the bad and none of the good.
The interaction between consultants
Okay, so in theory, if consultants’ recommendations are followed exactly and a turnkey system is built, in theory it should still be possible to imitate the medium costs of Denmark.
But in practice, the hallmark of consultants is private competition. This means there are different firms, and even though they are all broadly similar, they compete and each has a slightly different way of doing things and may have different recommendations for a specific project. And then each government agency in the United States hires a different consultant and the consultants clash and there is no way to resolve the conflict.
Seattle’s cost explosion in the last 10 years, going from semi-reasonable costs for U-Link to a world record for a majority-above-ground project for Ballard-West Seattle, comes from a somewhat different place from what we’ve seen in New York and Boston. For example, New York and Boston both have ample surplus extraction by local actors, but the extraction there happened before the plans were finalized and the Full Funding Grant Agreement was made; in the Seattle suburbs, one municipal fire department has demanded changes even after the FFGA and threatened not to certify the project. The issue of consultants there is likewise a new problem: a complex project – I think the Pacific Northwest intercity rail program but I forget – requires intergovernmental coordination and the different agencies hired different consultants, leading to substantial inter-contractor contention. The argument for privatizing state planning to large design-build contracts is that they avoid this contention, but here it’s recreated by the very presence of competition.
Nor is replacing competition with a single private consultant going to solve the situation. The private sector’s norms of how to deliver value depend on competition; all benchmarks used for how to successfully deliver to the customer are honed based on how to beat or at least match other firms that could get the contract if the firm fails. A private monopolist combines the worst aspects of the public sector (no competition) with those of the private sector (fundamentally adversarial relationship with the customer). As soon as a project is large enough that multiple agencies are involved, forcing them to all use the same consultant, even if the initial choice does feature competition between WSP, AECOM, Arup, and other such firms, means that for the duration of the project there’s such lock-in it has the same problems as a literal monopoly.
The way forward
If it’s not possible to successfully deliver infrastructure megaprojects through competition among private consultants or through a private monopoly, it follows that delivery must be done through the public sector. This means a public sector that is staffed up with thousands of permanent professional hires. Small cities can use big cities’ agencies or a federal agency as a public-sector consultant; in all cases, this must be domestic rather than international, since the social mission that makes many public monopolists good vanishes at the border and turns into predatory monopolistic behavior (for example, by SNCF toward other national railways).
Metropolitana Milanese, the infrastructure builder that also provides public-sector consulting services for the rest of Italy, has around 1,300 employees. The Anglo world can imitate that – never literally import the firm, but set up a similar construct, with advice by MM, RATP, and other public-sector engineering firms about how to do so and even some early hires. This needs to be done publicly and ostentatiously, to make it clear what’s going on for the sake of transparency and to lock in good changes. Instead of regulators who nudge, the state needs people who do; there is no alternative.
New York’s MTA Hates Transparency
The New York Post just published its piece, by Nolan Hicks, doing some construction cost comparisons. Nolan spoke to me multiple times on the subject of finding proper comparisons to New York’s subway station construction; he settled on the single most difficult Roman station, at the Colosseum, as well as a more prosaic station at Grand Paris Express and one on the Battersea extension in London. The goal was to look at the issue of New York’s overbuilt stations, with their full-length mezzanines and excessive back office space; New York’s stations turn out to be three to four times too expensive in his analysis.
So far, so good. But then there’s the official response to the story, which tells me that MTA head Janno Lieber is bad at his job – presuming that he views his job as about delivering good service, rather than stonewalling and kissing ass.
The Post quotes Lieber as saying, “you have to be careful with that subculture” and “those people get a lot of their cost information from the internet.” This is not too different from what he said when asked about our report by Jose Martinez: he got aggressive, said that we “group sourced” our data, and disclaimed responsibility for things that happened long ago, in the 2000s (Lieber at the time worked on the new World Trade Center).
People on Twitter are roasting Lieber about the phrases “that subculture” and “those people,” but I mind those appellations a lot less than what they are about. Lieber is in effect complaining that we use public sources for costs, which we access via the Internet, the same way we talk to other people in 2023. Using the Internet, for example, I can poke around for Swedish construction contracts, which are transparent with published lists of bidders and the winning bid, or I can look for historic German construction costs as reported in official channels and reputable media, and Marco can look for the same in Italy including publicly itemized costs, and Elif can look for the same in Turkey. What Lieber means when he says “information from the Internet” is really “articles in trade media and newspapers of record and detailed government reports, calibrated with some in-depth case studies to ensure we didn’t miss anything important.”
It jars him, perhaps because he’s used to secrecy. The idea that a report about the cost overruns of Grand Paris Express would just be out there, while the project was still going on, available to the public to review, may confuse Americans who are used to their country’s much lower level of transparency. In the US, everything requires affirmatively filing a freedom of information request that agencies can and often will deny on flimsy grounds. In Sweden, everything is online and I’ve been able to learn exactly how things work there from talking to not many people thanks to the wealth of public information about procurement strategy and individual contracts. The same is true of the issue of back office space and overbuilt station boxes – the MTA has not released blueprints, whereas in Sweden they’re available to the public in 3D.
Perhaps this is why Lieber talks to reporters with aggression and derision that fit would-be autocrats trying to put democratic media in its place. The idea that people would put all this information out there, voluntarily, seems weird to both, in the same way that a politician in an autocracy might find it jarring that politicians in democracies are subject to free media scrutiny.
This culture of secrecy cascades to itemized contracts. In our work, we’ve found that low-construction cost countries itemize their most complex rail infrastructure contracts, and the items are public. In the United States, contracts are fixed-price, and when agencies have itemized estimates as private benchmarks, they keep them from the public as a trade secret. MTA Construction and Development head Jamie Torres-Springer defended this system in November, saying that if the MTA revealed the numbers, contractors might use them as a floor.
Torres-Springer clearly stated a doctrine of the institutional culture that he and Lieber know. We can rate, overall, whether this culture is worth retaining, through seeing whether New York can build. It, of course, cannot. Lieber takes credit for delivering some projects for less than the budgeted amount, but the budget was inflated with large contingency figures; when someone promises to build something for $70 million and delivers it for $65 million, you don’t give credit for going under budget when other systems deliver it for $12 million. (These are all rough costs of making a subway station that is not a transfer wheelchair-accessible using three elevators in New York and some comparison cases respectively.)
Meanwhile, other systems, outside the high-cost Anglosphere (update 3-28: here is Ontario engaging in the same repulsive behavior toward Global News on the costs of the Ontario Line), can deliver. Germany doesn’t want to build much infrastructure unfortunately, but when it wants, it gets it done at reasonable if not low costs – and those costs are barely higher now in real terms than they were in the 1970s, having inched from maybe 150 million euros per km of subway to 200. Paris is building 200 km of mostly underground driverless metro, for about the same cost as one five-year MTA capital plan. Istanbul builds many metro lines all at once and may be the world’s top city in total route-length built this decade if Chinese investment slows down – Turkey is not a rich country but it has figured out how to build cheaply so that it can afford it. Seoul is expanding so rapidly, using so many different networks, that I can’t even track how much it builds. Italy not only can keep building infrastructure despite not having much money, but also managed to cut its real costs by adopting transparency as a core principle in the 1990s; contra Torres-Springer, contractors use published itemized costs as an anchor and not a floor.
But New York is the city that can’t, in the state that can’t. It treats a three-station subway expansion as a generational project. It clings to its way of doing things in face of obvious evidence that this way does not work; when it wants to do something different, it privatizes the state to consultants and huge design-build contractors, which has consistently raised costs wherever it is implemented. It’s not even aware of how success looks. Its leadership is rather like a Russian general who, seeing the army throw countless soldiers to take individual blocks of Bakhmut, population 70,000, insists things are going great and there is no need for anyone to learn anything about NATO standards, before ordering another wave of assault.
The press is ahead of the curve on this, since it does not need to kiss ass. I’ve been a source for New York media and for US-wide wonk networks for years, and the great majority of journalists I’ve spoken with, veterans and newcomers, generalists and specialists, have been curious and intelligent and could tell me important things I didn’t know before, including, in particular, reporters on this beat at all major city papers, such as Nolan. I sadly cannot say the same of MTA management: the career civil servants are good below the managerial level, the managers are hit-or-miss, and the political appointees are more miss than hit. The way the latter try to pull rank on good journalists like Martinez and Nolan is supercilious, authoritarian, and just plain nasty.
And if New York wants to avoid looking as ridiculous as that Russian general, it had better learn how successful cities do it, and invite in people who are intimately familiar with these cities to take in-house leadership jobs to implement the required reforms. This means, among other things, fostering a culture of openness and transparency. No more putdowns of journalists who ask hard questions, no more hiding behind NDAs and trade secrets, no more black boxes with no itemization beyond “this contract is $1 billion.” It’s easier than for Russia – the American field-grade officers who could do every Russian general’s job better don’t at all have Russia’s interests at heart, whereas the Continental European and East Asian transit managers who New York can bring it can be hired to have the MTA’s interests at heart, just as Andy Byford was. Learn from the best and face the reality that right now New York is the worst.